U-joint bearing/cross rebuild instructions
Moto Guzzi V700, V7 Special, Ambassador, 850 GT, 850 GT California, Eldorado, and 850 California Police models
Created:
Updated:
These instructions are not specific to Moto Guzzis, but may be helpful.
Thanks to Ralf Brinkmann for posting the link to this information on the old Yahoo! Loopframe_Guzzi news group (which has now moved to Groups.io).
Repair and Replacement of Wearing Parts on Propeller Shafts
Extracted from Klein Gelenkwellen.
All joints are fully dismantable and designed for dismantling without special tools.
However for safety reasons, the following work should be carried out only by competent work shops. In case of doubt please ask us.
When dismantling a propeller shaft, first check whether the positions of forks 1 and 2 are marked by arrows (see Fig. 2); if the marking is covered with paint, these sliding parts should be clearly marked together.
We strongly recommend not replacing damaged bearings individually as in most cases the pins on the universal joint will also be damaged. It is therefore advisable to replace only complete universal joint fittings (Fig. 7). In the case of wear in the sliding profile, splined shafts and hubs should always be replaced together. The wear limit for fast running shafts is achieved when play is perceptible in the installed position.
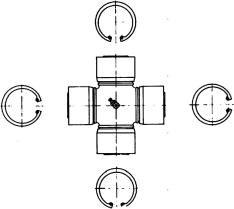
Photo courtesy of Klein Gelenkwellen.
3.1 Dismantling a Joint
- Remove all four circlips with circlip pliers.
- Push the universal joint and bushes to one side using a press (see Fig. 8a).
- Clamp the projecting bush in a screw vice and withdraw the bush with light hammer blows on the fork (Fig. 8b). Do not reuse bearing bushes with thin walls.
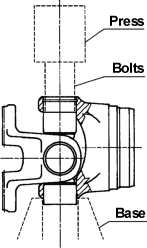
Photo courtesy of Klein Gelenkwellen.

Photo courtesy of Klein Gelenkwellen.
3.2 Assembling a Joint
- Press in the bearing bushes exactly in line with their centrelines, without tilting them.
- Fit circlips so that the universal joint can be easily moved. To achieve this, circlips of various thickness are used and if absolutely necessary a thicker circlip can be ground to the required dimension. The clearence at the ends of the pins should be adjusted so that the bending moment of the flange in both axes does not exceed 4 Nm, without letting the flange drop down on his own accord.
- Check that the joint runs true. To do this, mount the propeller shaft on the flange fitting and check the tube with a dial gauge. Maximum permissible runout is 0.1 mm. For running speeds under 1500 RPM this check will in most cases avoid the need for balancing and for speeds above 1500 RPM it considerably shortens the balancing process.
In the case of motor vehicles, the running speed is generally above 1500 RPM. Propeller shafts for this application must be dynamically balanced. The balancing speed should always be 10-15% above the maximum speed occurring in service.
The acceptable balance is laid out in DIN ISO 1940.